Quality Assurance in Third-Party Manufacturing Pharma Companies in India
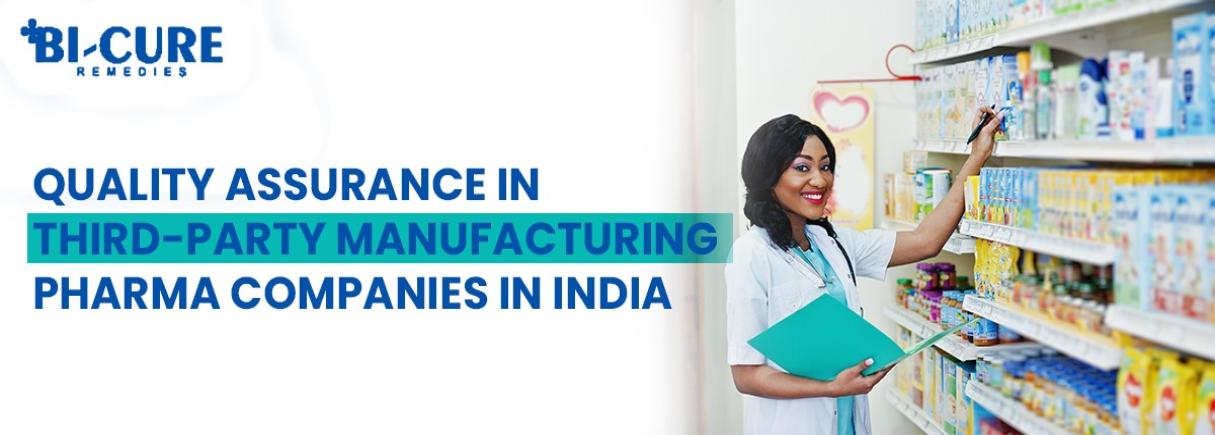
Get In Touch With Us
Download Brochure
India has emerged as one of the world's largest pharmaceutical manufacturing hubs. In 2025, the pharmaceuticals market in India is predicted to generate US$13.48 billion.
Third-party pharmaceutical manufacturing in India is the centre of this expansion. It is often known as contract manufacturing. These companies produce medicines for other businesses, allowing them to concentrate on marketing rather than investing in manufacturing facilities. India is seeing rising demand for third-party pharmaceutical manufacturers.
However, maintaining high-quality standards is crucial for assuring product safety and building consumer trust. In this blog, you will explore why quality assurance is critical in third-party manufacturing.
Importance of Quality Assurance in Third Party Pharmaceutical Manufacturing
Quality assurance (QA) is essential in third-party pharmaceutical manufacturing. The primary goal is to guarantee that the products are safe, effective, and consistent. High-quality standards not only preserve public health but also contribute to a company's reputation. If product quality is compromised, it may result in recalls, legal issues, and a loss of consumer trust.
Additionally, adherence to Good Manufacturing Practices (GMP) is vital. These practices provide quality standards for manufacturing, equipment, and employee behaviour. A strong QA system avoids errors and assures that each batch meets the same high standards. Even tiny differences can have serious effects on patients and businesses.
Key Quality Control Measures Adopted by Third Party Pharma Manufacturers in India
Third-party pharmaceutical producers in India use a variety of quality control procedures to ensure that their products are consistent.
Raw Material Selection and Vendor Qualification
Quality begins with purchasing raw materials from certified vendors. Manufacturers only engage with vendors who stick to strict product safety criteria.
In-process quality control (IPQC)
Manufacturers track manufacturing at various levels. This includes testing formulations, dosing accuracy, and environmental factors such as temperature and humidity.
Finished Product Testing
After production, final products are thoroughly tested to ensure they meet pharmacopoeial requirements, including purity, potency, and stability.
Stability Studies
Stability tests assess the product's effectiveness in a variety of environmental circumstances (such as temperature and humidity) to assure long-term performance.
Packaging and labeling checks
Manufacturers ensure that packaging and labelling attach to regulatory requirements. This avoids counterfeit items and provides clear instructions to buyers.
Facility Hygiene and Personnel Training
A clean, controlled environment is critical for preventing contamination. Regular hygiene checks and employee training are critical for ensuring safety.
Regulatory Compliance and Certification
To maintain good product quality, a third party medicine manufacturer in India must stick to a number of regulatory norms. Key certificates include:
WHO-GMP: It stands for World Health Organization's Good Manufacturing Practices. This ensures that producers use internationally recognized production techniques.
ISO 9001:2015: Indicates that a corporation has a quality management system that prioritizes improvement and customer satisfaction.
Schedule M Compliance: This regulation, issued under the Drugs and Cosmetics Act of India, establishes necessary requirements for pharmaceutical product manufacturing in the country.
Frequent audits and inspections ensure manufacturers maintain compliance with these criteria. This protects the integrity of pharmaceutical products and ensures that producers satisfy both national and international criteria.
The Role of PCD Pharma Franchise in Quality Assurance
PCD (Propaganda-Cum-Distribution) Pharma Franchise enterprises also play an important role in quality control. They collaborate with third-party manufacturers who have a great compliance record.
By selecting manufacturers with proven quality control methods, PCD franchise companies may provide their consumers with safe and trustworthy products, hence increasing consumer trust.
Conclusion
Quality assurance is critical in third-party manufacturing pharma company in India. Implementing strong quality control systems, following laws, and focusing on continual improvement guarantees that products are safe and effective.
Working with reputable suppliers ensures that PCD Pharma Franchise companies provide reliable products to their customers. As the pharmaceutical industry grows, maintaining high-quality standards will become increasingly important for both makers and customers.
Frequently Asked Questions
What is quality assurance in pharmaceutical manufacturing?
Quality assurance in pharmaceutical manufacturing ensures that products meet required standards and regulations, focusing on consistency, safety, and efficacy through systematic processes and audits.
Who is the GMP certified third-party manufacturer?
A GMP-certified third-party manufacturer complies with Good Manufacturing Practices (GMP) regulations to produce pharmaceutical products on behalf of another company while ensuring product quality and safety.
Who QC is part of GMP?
Quality Control (QC) is an essential part of GMP, responsible for testing and ensuring that raw materials, in-process materials, and final products meet quality specifications and regulatory standards.
Importance of Quality Assurance in Third Party Pharmaceutical Manufacturing
Quality assurance (QA) is essential in third-party pharmaceutical manufacturing. The primary goal is to guarantee that the products are safe, effective, and consistent. High-quality standards not only preserve public health but also contribute to a company's reputation. If product quality is compromised, it may result in recalls, legal issues, and a loss of consumer trust.
Additionally, adherence to Good Manufacturing Practices (GMP) is vital. These practices provide quality standards for manufacturing, equipment, and employee behaviour. A strong QA system avoids errors and assures that each batch meets the same high standards. Even tiny differences can have serious effects on patients and businesses.
Key Quality Control Measures Adopted by Third Party Pharma Manufacturers in India
Third-party pharmaceutical producers in India use a variety of quality control procedures to ensure that their products are consistent.
Raw Material Selection and Vendor Qualification
Quality begins with purchasing raw materials from certified vendors. Manufacturers only engage with vendors who stick to strict product safety criteria.
In-process quality control (IPQC)
Manufacturers track manufacturing at various levels. This includes testing formulations, dosing accuracy, and environmental factors such as temperature and humidity.
Finished Product Testing
After production, final products are thoroughly tested to ensure they meet pharmacopoeial requirements, including purity, potency, and stability.
Stability Studies
Stability tests assess the product's effectiveness in a variety of environmental circumstances (such as temperature and humidity) to assure long-term performance.
Packaging and labeling checks
Manufacturers ensure that packaging and labelling attach to regulatory requirements. This avoids counterfeit items and provides clear instructions to buyers.
Facility Hygiene and Personnel Training
A clean, controlled environment is critical for preventing contamination. Regular hygiene checks and employee training are critical for ensuring safety.
Regulatory Compliance and Certification
To maintain good product quality, a third party medicine manufacturer in India must stick to a number of regulatory norms. Key certificates include:
WHO-GMP: It stands for World Health Organization's Good Manufacturing Practices. This ensures that producers use internationally recognized production techniques.
ISO 9001:2015: Indicates that a corporation has a quality management system that prioritizes improvement and customer satisfaction.
Schedule M Compliance: This regulation, issued under the Drugs and Cosmetics Act of India, establishes necessary requirements for pharmaceutical product manufacturing in the country.
Frequent audits and inspections ensure manufacturers maintain compliance with these criteria. This protects the integrity of pharmaceutical products and ensures that producers satisfy both national and international criteria.
The Role of PCD Pharma Franchise in Quality Assurance
PCD (Propaganda-Cum-Distribution) Pharma Franchise enterprises also play an important role in quality control. They collaborate with third-party manufacturers who have a great compliance record.
By selecting manufacturers with proven quality control methods, PCD franchise companies may provide their consumers with safe and trustworthy products, hence increasing consumer trust.
Conclusion
Quality assurance is critical in third-party manufacturing pharma company in India. Implementing strong quality control systems, following laws, and focusing on continual improvement guarantees that products are safe and effective.
Working with reputable suppliers ensures that PCD Pharma Franchise companies provide reliable products to their customers. As the pharmaceutical industry grows, maintaining high-quality standards will become increasingly important for both makers and customers.
Frequently Asked Questions (FAQs)
What is quality assurance in pharmaceutical manufacturing?
Quality assurance in pharmaceutical manufacturing ensures that products meet required standards and regulations, focusing on consistency, safety, and efficacy through systematic processes and audits.
Who is the GMP certified third-party manufacturer?
A GMP-certified third-party manufacturer complies with Good Manufacturing Practices (GMP) regulations to produce pharmaceutical products on behalf of another company while ensuring product quality and safety.
Who QC is part of GMP?
Quality Control (QC) is an essential part of GMP, responsible for testing and ensuring that raw materials, in-process materials, and final products meet quality specifications and regulatory standards.